
Inspired by Voron, Completely Redesigned from the Ground Up. . .
Image above is most, but not all required 3D printed parts to make a Voron V2.4 3D printer.
Design objectives of this project:
Less parts to be 3D printed during the construction
Design a much larger printer than the Voron V0 (see image below)
Able to 3D print stronger and more exotic materials, requiring hotter printing temperatures
First, some definitions:
Voron is a community based line of 3D printer designs. As a community they have matured into producing fast, accurate and capable 3D printers you build yourself. They match the performance of commercially produced printers that are 3x their cost. Each printer design relies heavily on 3D printed parts, has a thorough bill of materials and a list of recommended suppliers.
It is up to you to procure all parts and the designs rely heavy on 3D printed parts in the construction. Once completed you have a 3D printer that can create production ready parts 24/7 with very little maintenance.
Hotend is the group of components that heats up and extrudes the molten plastic to be added layer by layer for a FFF ( Fused Filament Fabrication) style printer. They normally use a spool of 1.75mm or 2.85mm diameter filament.
Hotbed is the heated bed surface in-which the 3D model is built on. Hotbeds can either be fixed or move in one or more axis.
3D printers have similar kinematics as CNC (Computer Numerical Control) mills that machine parts.
PLA (Polylactic Acid) plastic filament is the most widely used material for small and hobby type 3D printers. It requires lower temperatures for the Hotend and Hotbed.
ABS (Acrylonitrile Butadiene Styrene) is a widely used plastic in everything from computer housings, mice, keyboards, appliances of every type and most car interior parts.
These definitions will be used throughout this page.
Why This Project:
I'd like to make the Voron V2.4 but my heavily modified BIQU B1 printer was designed to make PLA parts and is not up to the task. The Voron 3D printers are only designed to use well printed ABS plastic parts. The ABS injection modeled parts found all around you are made at temperatures 260°C and are held at temperatures of 90-110°C for 3 to 8 hours. Modifying a hobby 3D printer Hotend to 260°C and sustaining enclosure temperature of 55°C was achievable (see my heavy modified 3D printer (link). With FFF printers as each layer is laid down it starts to cool off quickly. Even with the best tuned printing the mass of the part being printed cools off too quickly, causing great stress concentrations. The part can warp, break at the layer lines or can even fully break off the Hotbed, destroying the part. I have done extensive testing with even visually good looking parts. These have failed at the layer lines far below the yield strength of the ABS plastic.
I have done extensive testing with even visually good looking parts fail at the layer lines far below the yield strength of the ABS plastic.
Bring up the heat!
It is difficult to keep the control electronics from overheating and maintain the correct ambient temperature in the enclosure. The trick is to keep the whole structure cool even as it's heat soaking. I can only print a few 3D parts at a time before a long cool down period.
The machine, making the machine, making the machine...
The plan has been to modify my current 3D printer to make the next far more capable 3D printer, to make a much larger and faster 3D printer. Both the 2nd and 3rd 3D printers are in the process of completion.
Size Comparison and Motion System
My 3D printer design is more than twice the size of the Voron V0 yet retains the minimal amount of the printed components.
The Hotend motion system was brilliantly designed and could be scaled up but the Hotbed axis was, confirmed by the engineers that designed it, not to be so simple. 80% of the parts had to be redesigned."
Design Community Inspiration
There is a large international Voron community making changes to an already well designed system. Since my design was so different from the original system I took a lot of inspiration from the many helpful and intelligent individuals of that community.
More Information, More Control
The Voron V0 has no controls on the 3D printer itself. Everything is controlled remotely. I wanted to aid in the many tasks that make the 3D printing work-flow more efficient and added a 2nd controller electronic board and a touch screen interface.
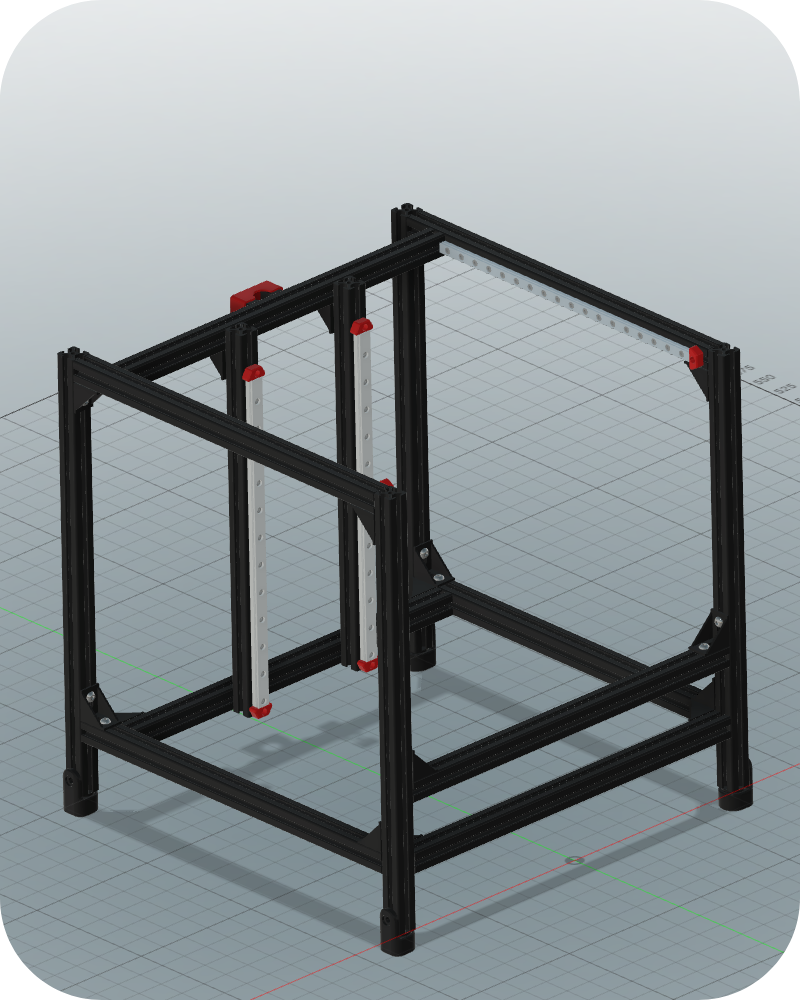
I utilized larger, stronger aluminum extrusion profiles and larger linear rails while staying with the overall outline of the V0 frame.
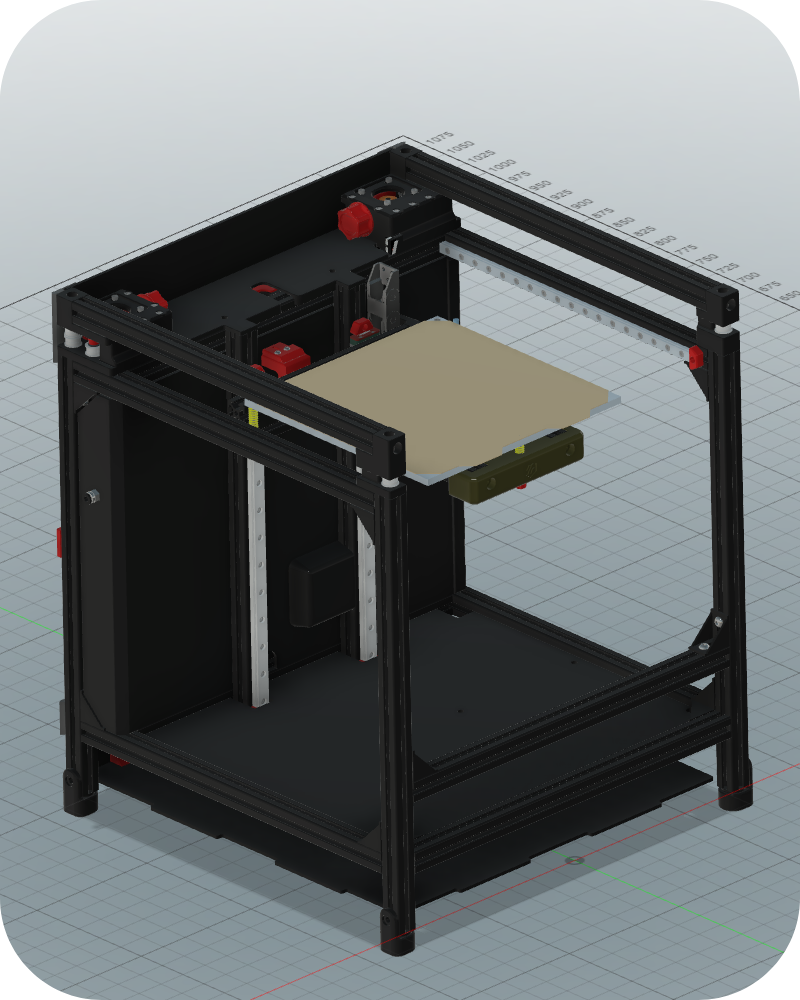
All components had to be redesigned to fit the larger sized and shaped profiles
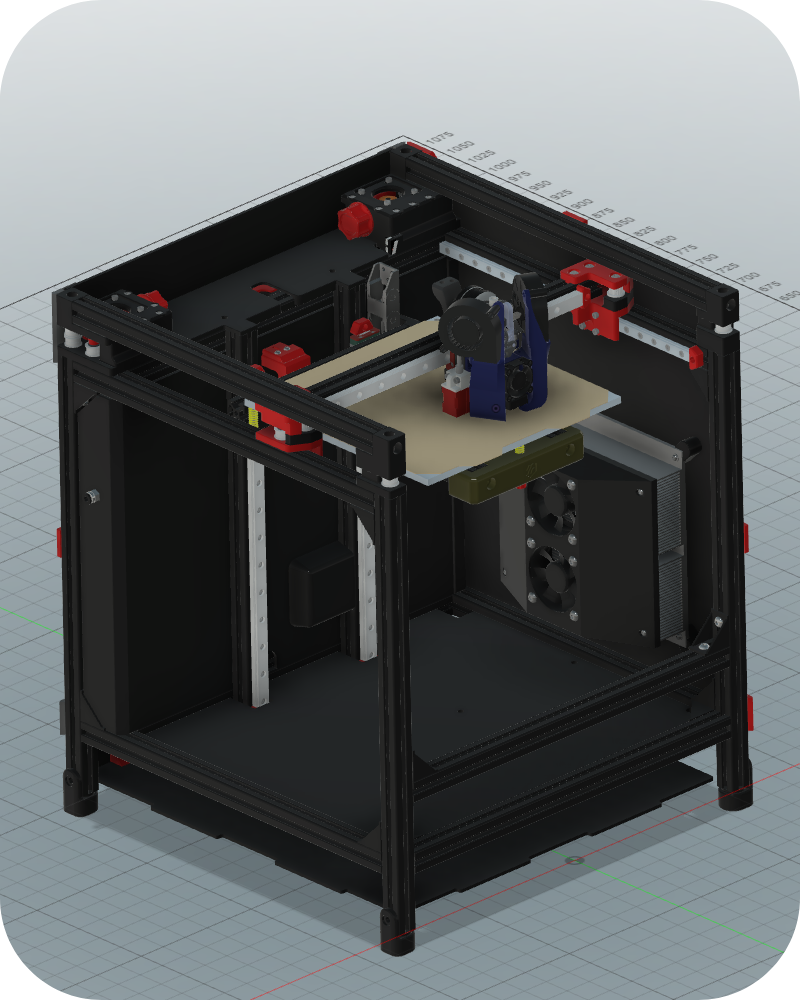
The Hotbed has 4x the surface area and is much heavier than the V0, forcing me to cleverly engineer around the greater moment arm.
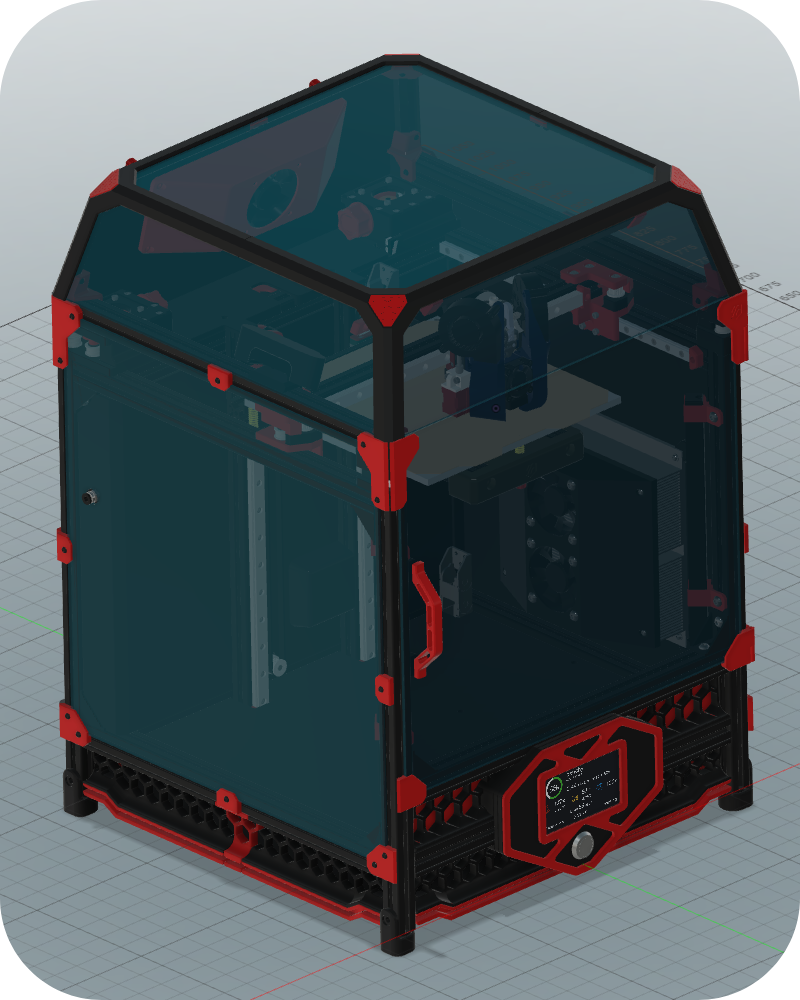
I wanted to be able to print exotic filaments, requiring greater temperatures from the Hotend, Hotbed and the printer enclosure to keep the plastic at the correct heated state uniformly throughout printing. The 8mm thick walls with honeycomb aluminum composite are required to prevent both warpage of the 3D printer assembly and damage to the control electronics.
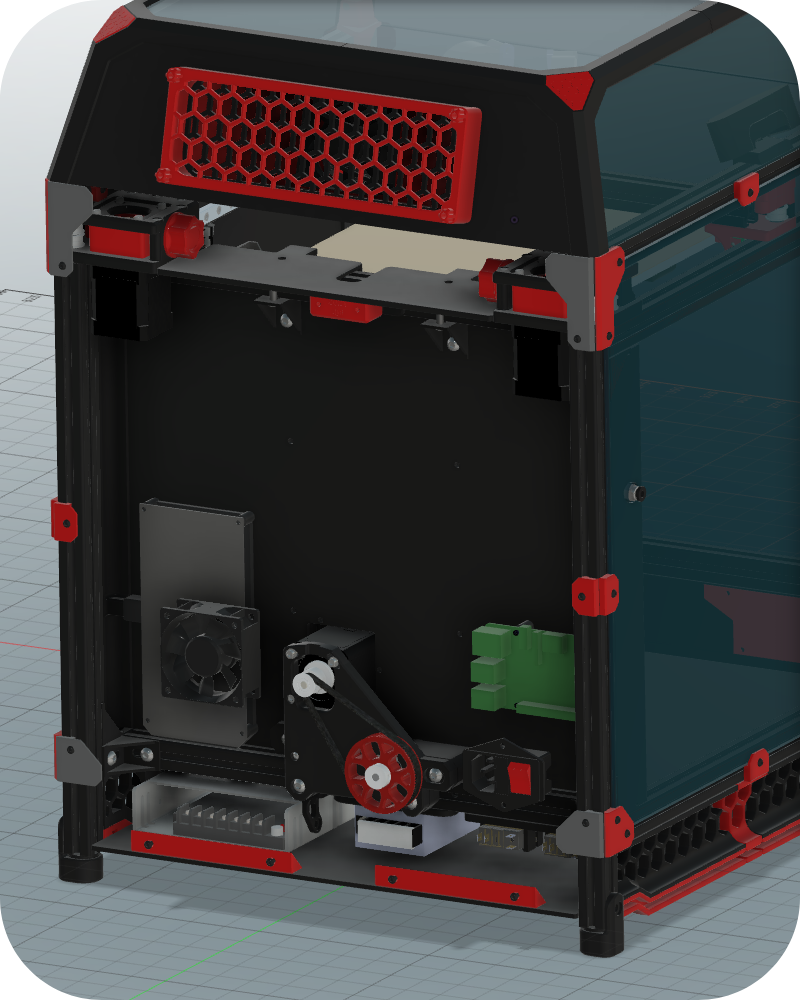
Different power supplies are mounted in the lower area: 120V to 48V, 48V to 12V and 48V to 5V to power the different electronics and accessories.

The larger size means more room for the control electronics. All electronics are double insulated from the hot enclosure side.
This project had many engineering challenges. The intent of the design was to learn what works, what doesn't work, and why doesn't it work. Through extensive research I've overcome the failures to iterate a better design.
This page will be updated. . .
Many components and assemblies have been completed since the first pictures were taken of the bare aluminum extrusions. Please re-visit this page for updates.